ENGDYN - crankshaft analysis
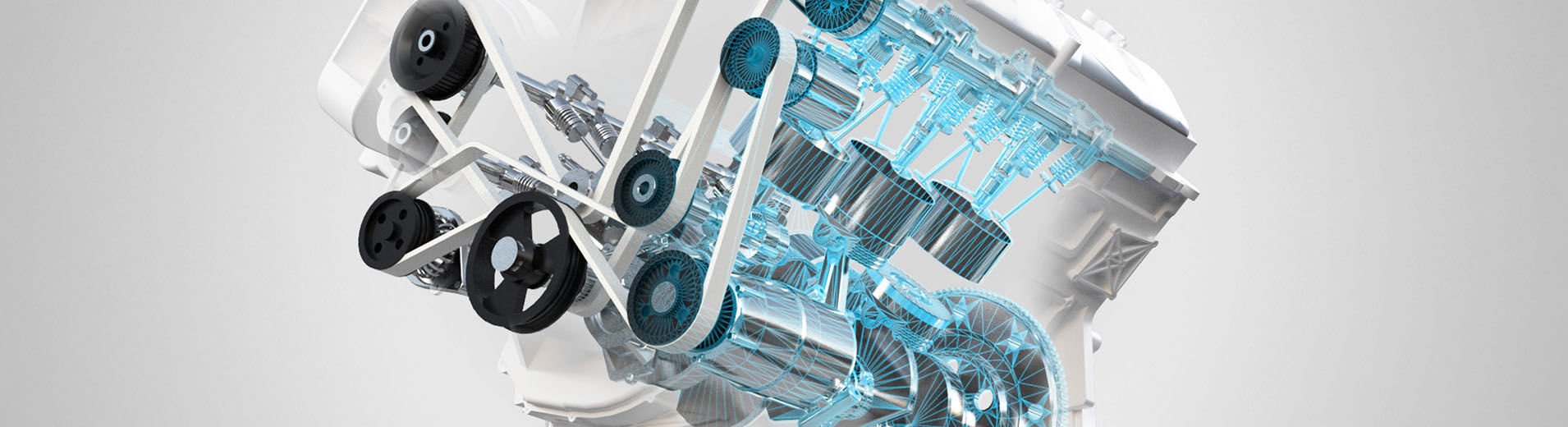
ENGDYN provides two methods of solution for predicting crankshaft durability, incorporating both a classical approach using simple beam theory as well as a more advanced finite element (FE) approach for more definitive studies. ENGDYN calculates both the quasi-static and vibratory loads on the crankshaft, and automatically sets up the necessary FE analysis. With its inbuilt fatigue module, ENGDYN can also provide both multi-axial and Goodman durability calculations for the key design areas on the crankshaft.
Specific crankshaft applications
- Crankshaft stress, fatigue and durability analysis
Key features
- Concept-level and fully 3D FEA solutions
- Automatic loading of FE models for solution
- Additional external loads
- Separation of static and vibration loading
- Effect of surface treatment on material strength
- Stress concentration and fatigue notch factors considered
- Uni-axial and multi-axial fatigue algorithms included