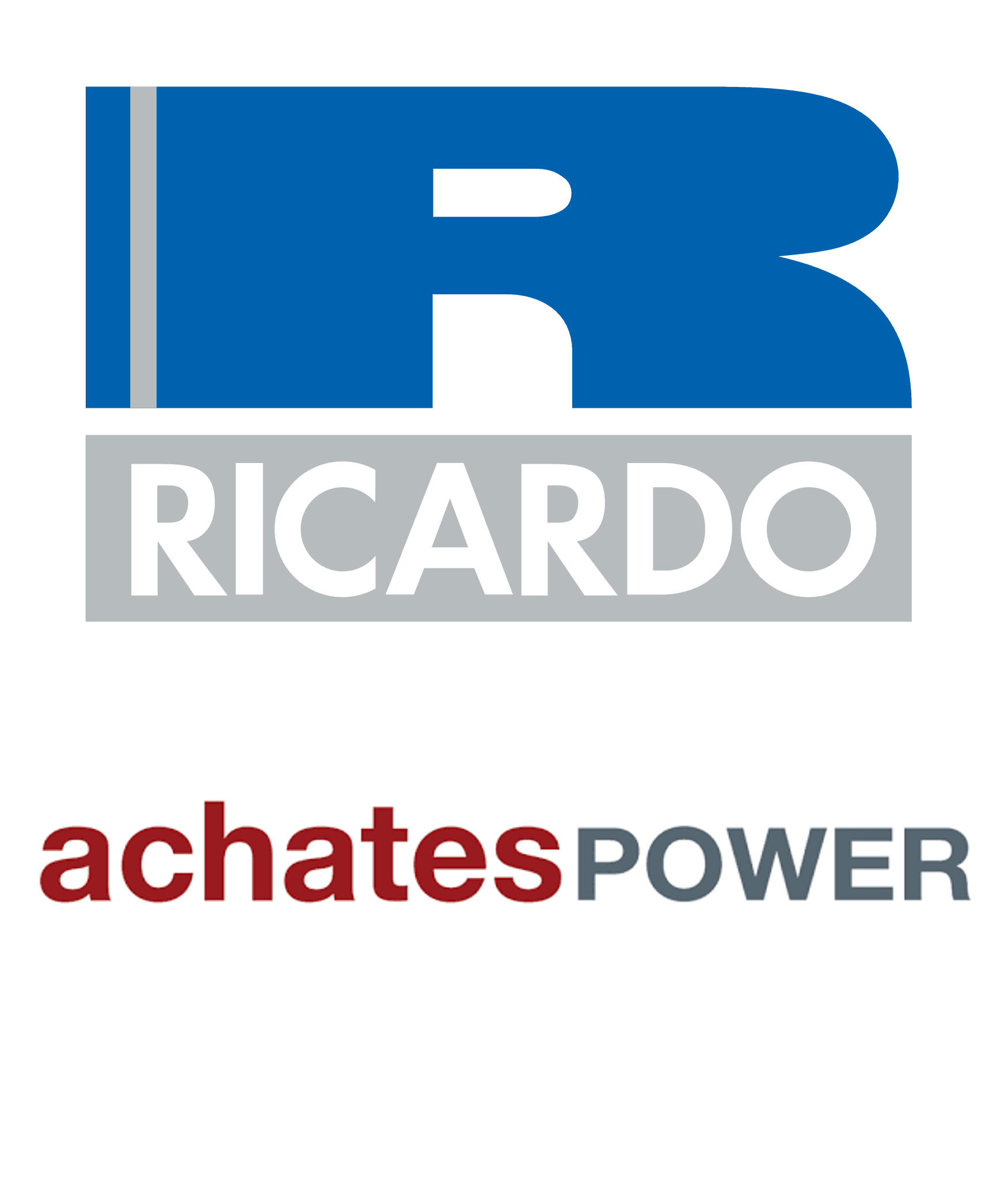
ENGDYN
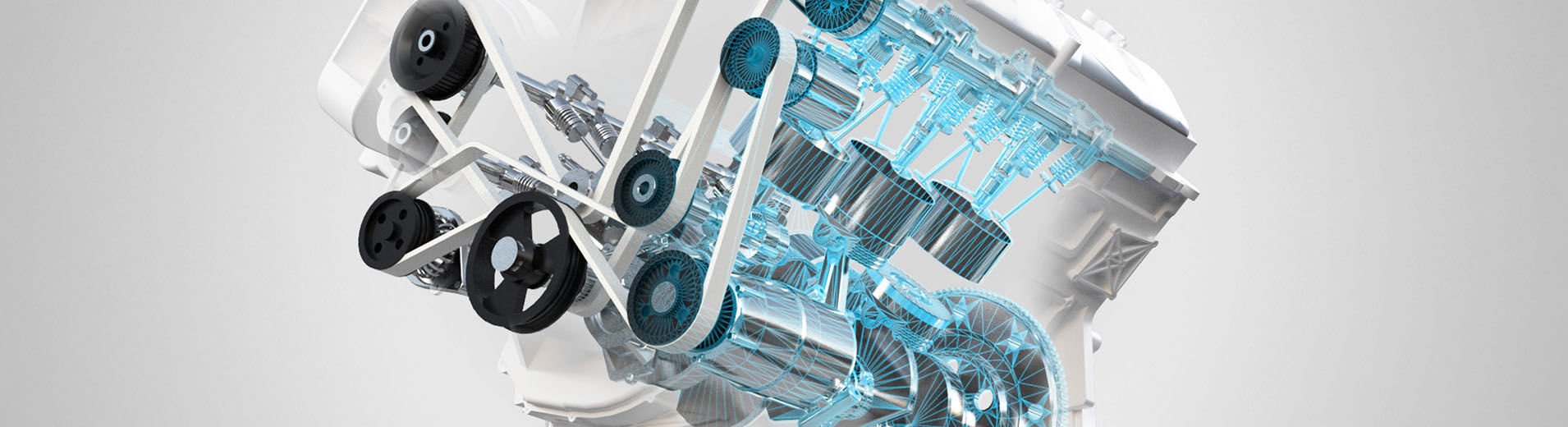
Essential 3D analysis for engine developers
ENGDYN is a dedicated 3D engine analysis tool essential to the design and development of the crank train, engine structure and associated components including bearings, connecting rods and engine mounts. By offering a range of complexity for components, oil film models and solvers, ENGDYN can be used throughout the entire development programme, from concept through to production. A key benefit of ENGDYN is that users can quickly and efficiently design and optimise engines.
How it works
ENGDYN's application range expands by linking with other packages such as VALDYN, and MATLAB Simulink® to perform fully coupled co-simulations with data passed between the codes at each time step. The links with VALDYN are fully integrated and allow systems such as the front-end accessory drive/rear-end accessory drive (FEAD/READ) or camshaft assemblies to be fully integrated with the powertrain analysis.
Key features
- Hierarchy of models and solution methods within a single easy-to-use graphical interface
- Kinematic and dynamic solvers
- Mobility-based bearing model for rapid kinematic and dynamic solutions
- Advanced mass-conserving elastohydrodynamic (EHD) lubrication model for detailed bearing analysis
- Hydrodynamic and boundary lubrication models
- Link with VALDYN for valvetrain, timing drive and auxiliary drive loading
- Link to FEARCE for automated loading of finite element (FE) engine models
- Integrated FEARCE solver for FE matrix reduction
- 3D graphical interface for rapid model generation and results presentation
- Vibro-acoustic analysis using integrated acoustic solver
Our insights
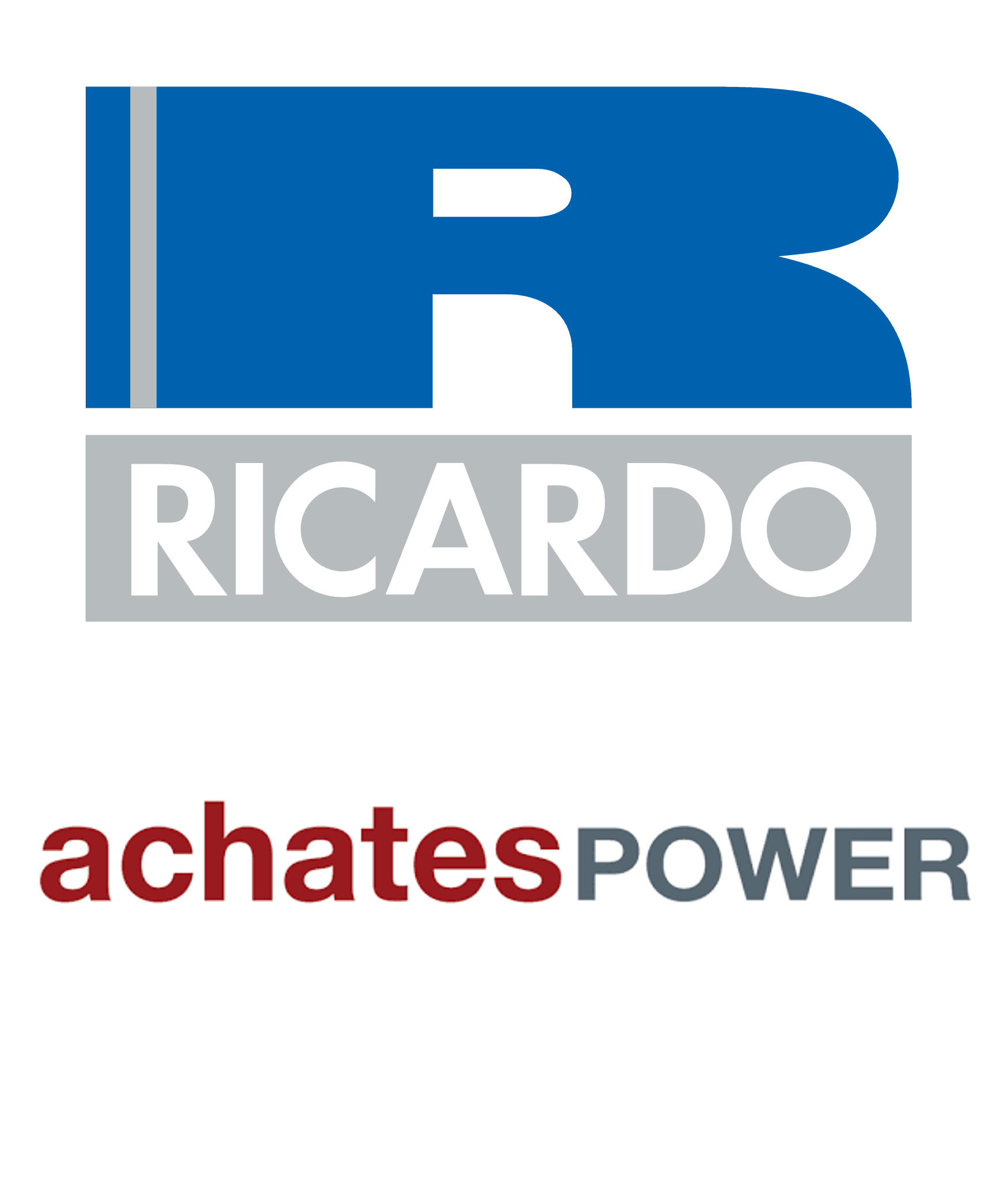
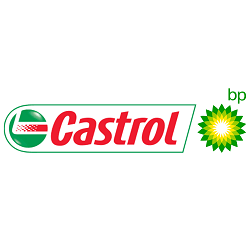
From asperity to fuel economy – a digital friction study
Conference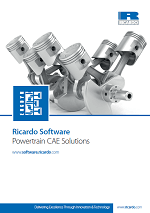
ENGDYN Flyer
Brochure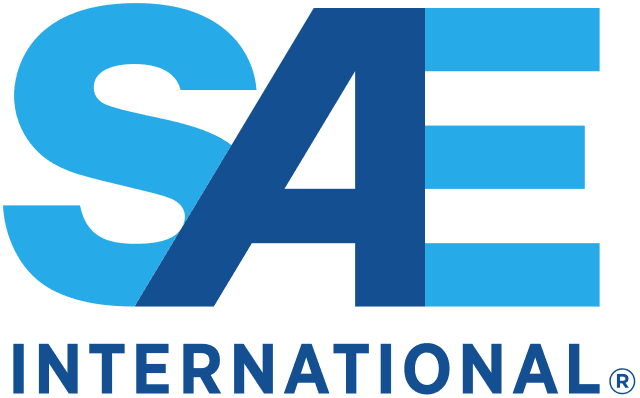