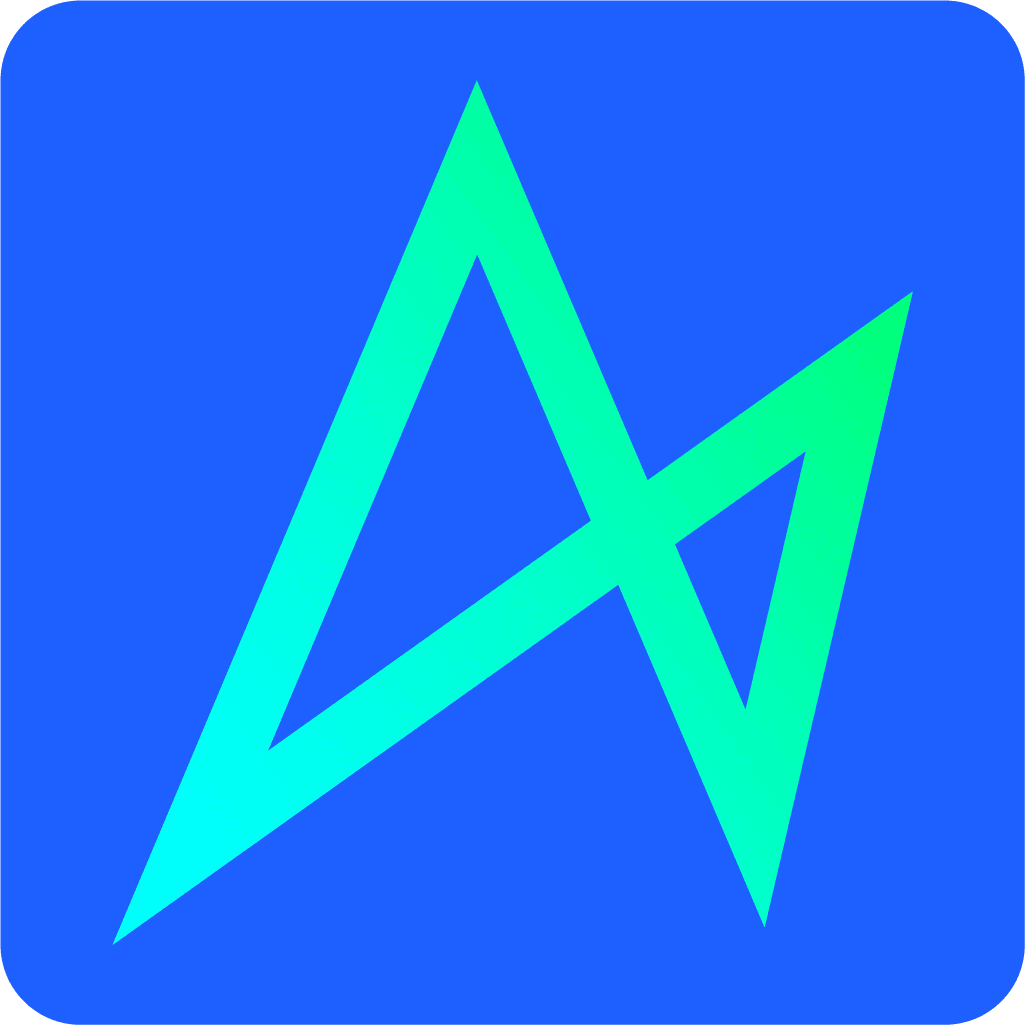
Crankcase Flow Modeling for a Racing Motorcycle Engine

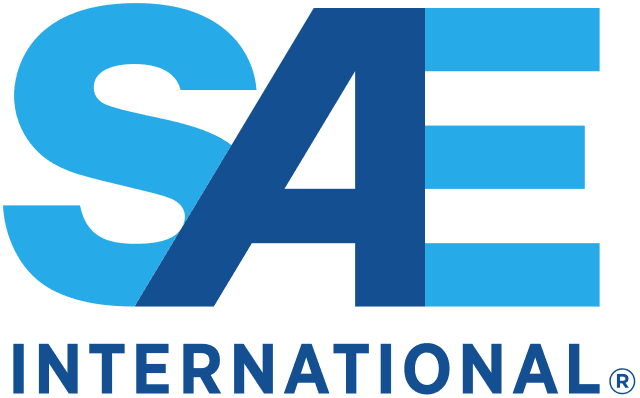
Crankcase Flow Modeling for a Racing Motorcycle Engine
When designing a sump system for a high performance engine the choice of the size of the inter-bay breathing passages is critical. The passages should be chosen to minimize the crankcase pumping loss and oil aeration while still maintaining adequate removal of blow-by gases and a good block structure.
This paper presents an approach to the modeling of engine crankcase gas flow using Ricardo WAVE software. The model was developed during the design of a dry sump version of a racing engine and was validated using pressure and blow-by data. The model was used to quantify gas velocities, pressure fluctuations and power loss due to the pumping of crankcase gas.
The effects of changes to a series of parameters such as breather hole size, sump volume, engine size and crankcase compression ratio were quantified.
This approach provides useful guidance in the design of dry sump systems at the concept design stage.
Realis Simulation, formerly Ricardo Software.
Our insights
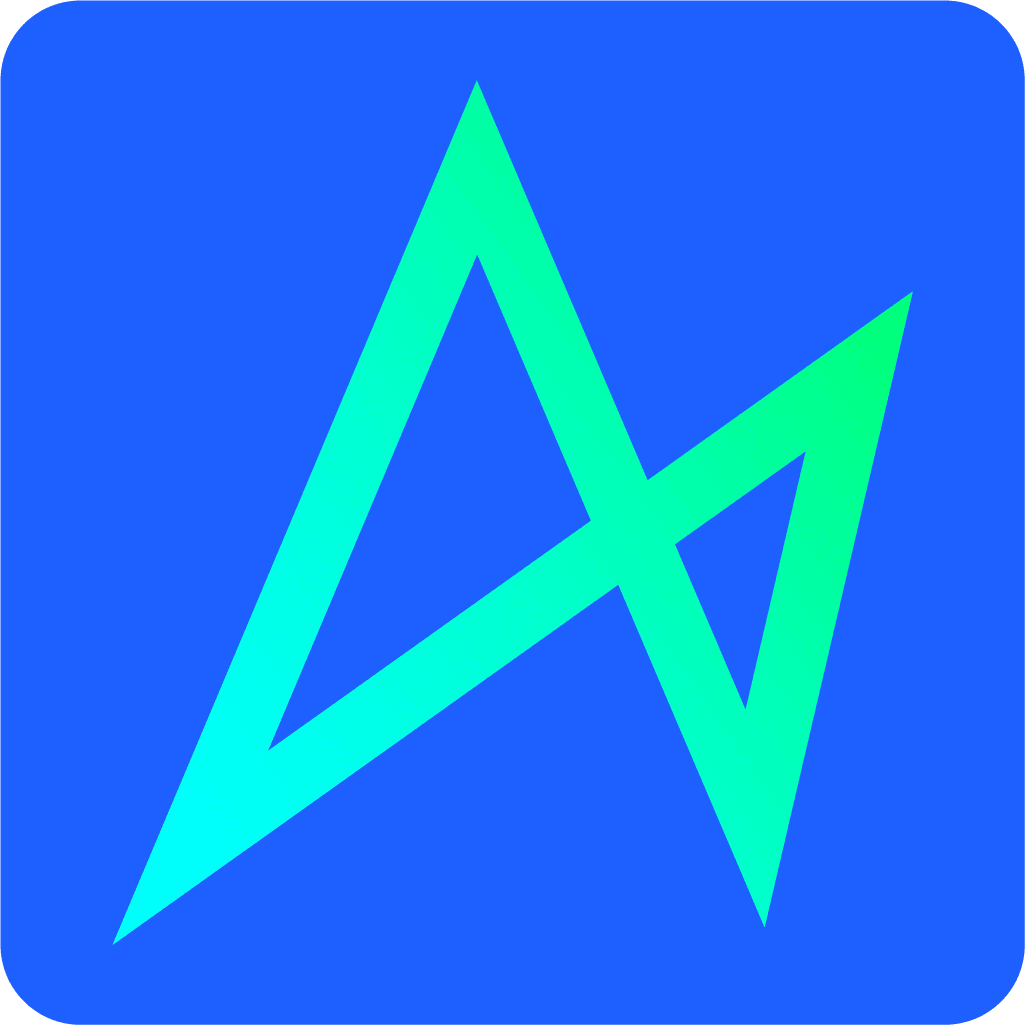
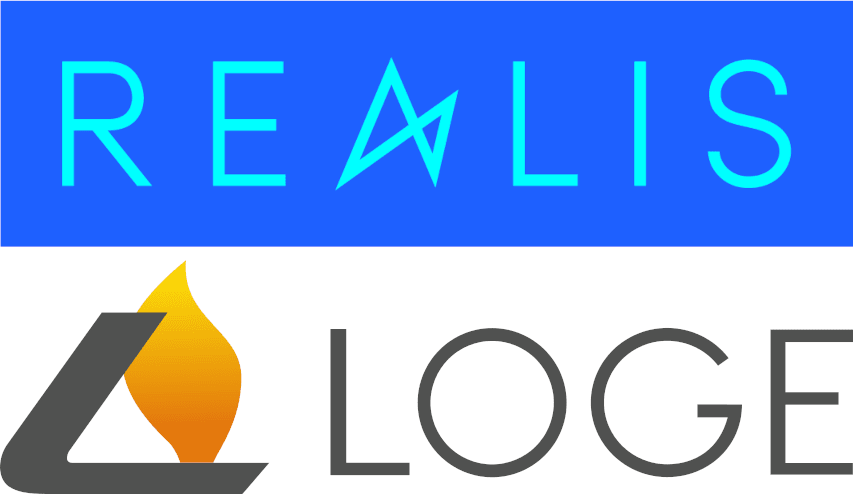
Accelerated accurate detailed kinetics in 3D CFD VECTIS simulations
Conference