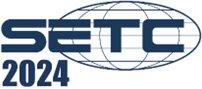
Virtual calibration
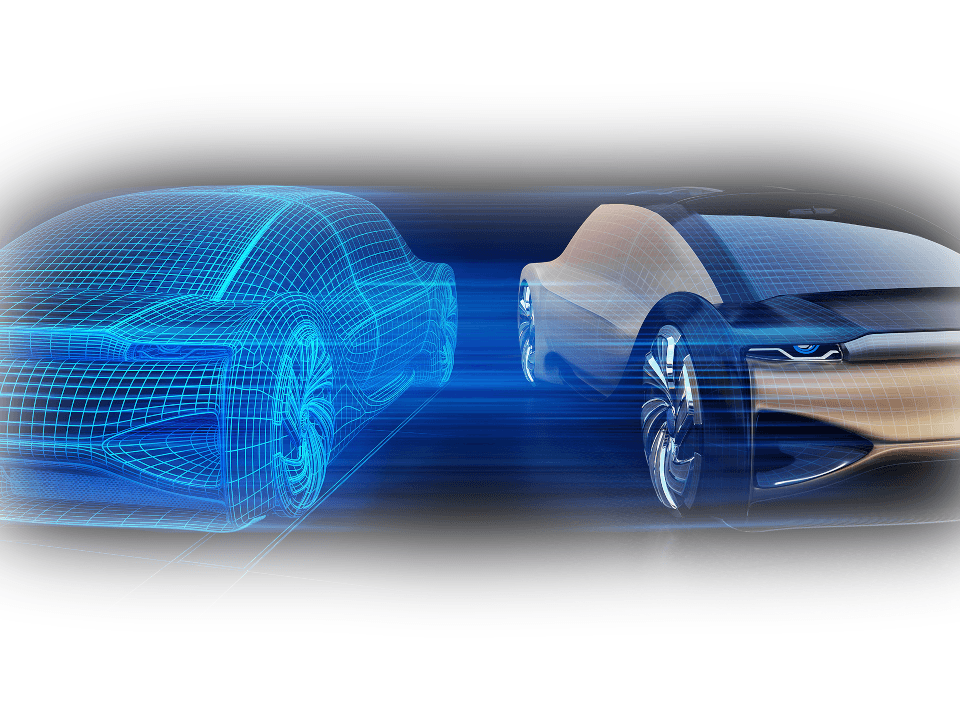
Efficient engine calibration using simulation
As manufacturers are being required to bring new innovations to market with tighter regulations and increasing financial constraints, there is a need to reduce the dependency on physical testing by simulating tasks which carry the highest costs. The use of a real-time digital twin tool allows the virtualisation of engine calibration, using limited physical data obtained by testing supplemented by simulated data from the digital twin - saving time and money whilst maintaining the quality and robustness of the results.
The savings from a single virtual calibration work package can pay for the software investment in one go by reducing the cost of data acquisition by as much as 70% and the time for data acquisition by up to 40% based on representative case studies. A traditional physical only approach requires thousands of test points to create a calibration model. By contrast efficient calibration uses limited correlation data to tune the plant model which generates the calibration simulation results, drastically reducing the amount of measured data required.
Realis virtual calibration software using virtual data acquisition cuts the required resources needed for physical testing by predicting vehicle performance for simulated calibration profiles using a digital twin.
Our insights
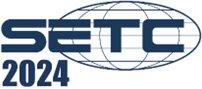
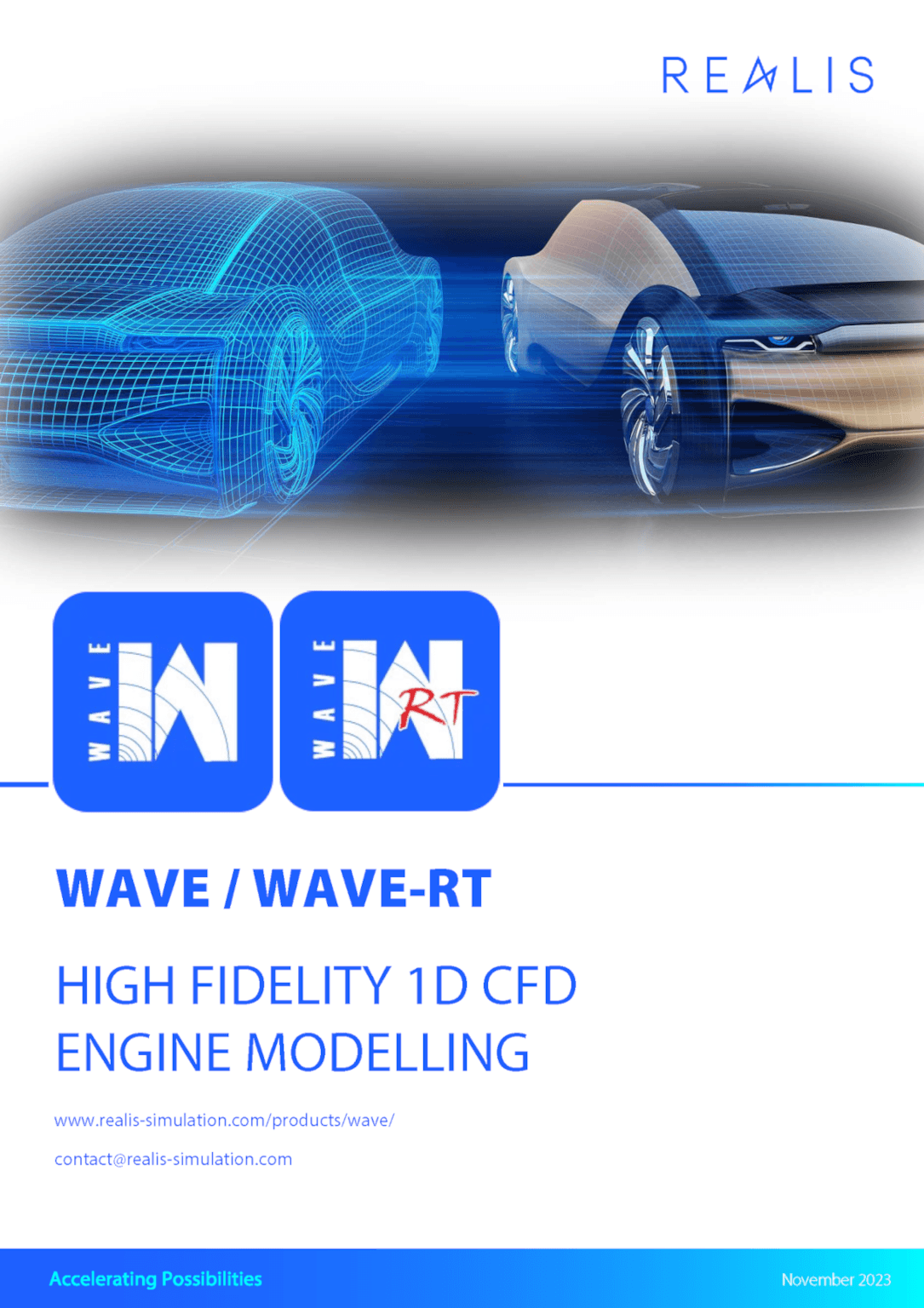
WAVE
Brochure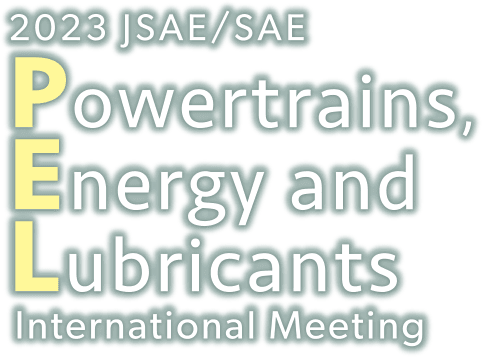
Highly efficient development of powertrain systems using 1D Real-Time Engine Model
Technical Paper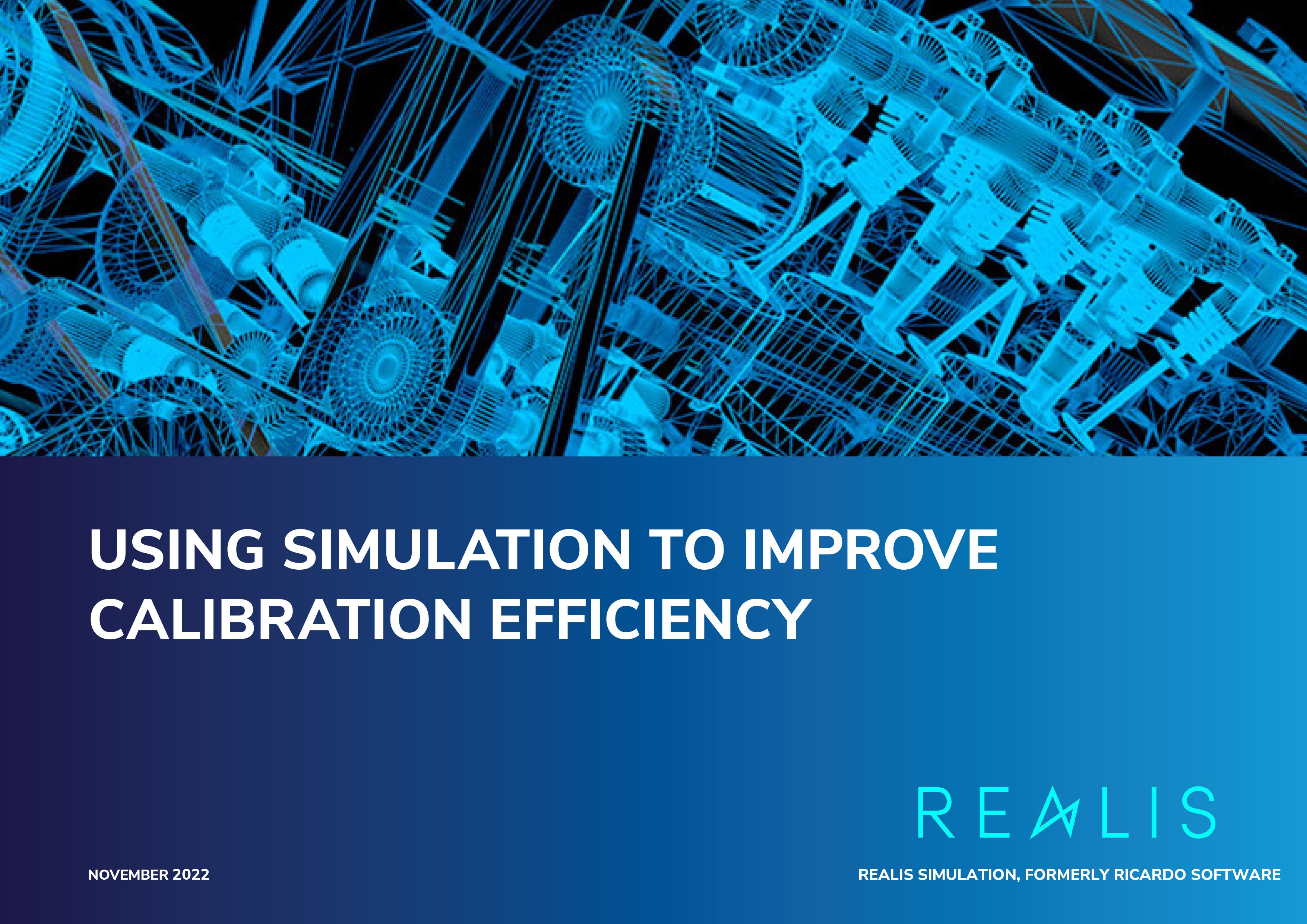